Posted by Zosi Team
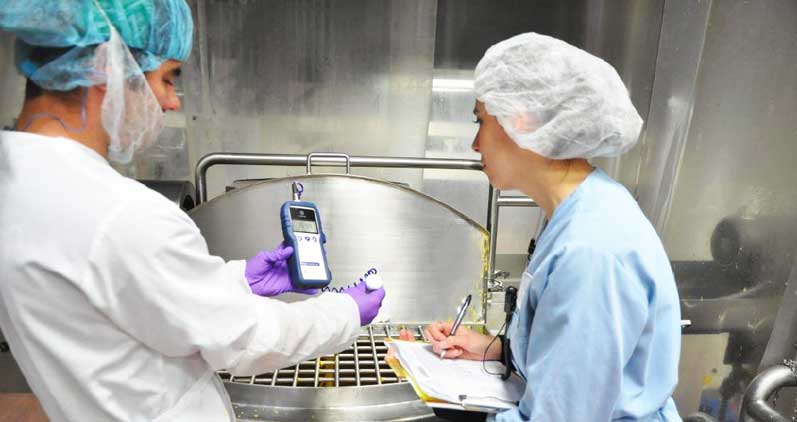
In the food industry, leaders must create and maintain a food safety culture that empowers teams to identify and respond to issues before they become serious problems. The most effective path toward this culture is through a risk mitigation mindset.
Risk mitigation is the process of understanding certain risks and threats, accepting that they exist, and taking the appropriate measures to reduce their effects in case they happen. There are four ways to mitigate risks:
- Transferring risk allocation between different parties to address threats, such as transferring the responsibility of a pathogen-free ingredient to your suppliers.
- Accepting certain risks until they can be adequately addressed. This could be using old equipment that you know is difficult to clean and sanitize until the budget allows for a replacement.
- Avoiding risks whenthe consequences of certain risks are too high to mitigate, such as preventing Salmonella by heating chicken to an internal temperature of 165 degrees.
- Monitoring risks by keeping a close eye on different processes and teams to assess threats as they develop, such as analyzing environmental swabs monthly for Listeria.
To foster a risk mitigation mindset, leverage these seven best practices.
- Teach the “why” behind the “what.”
- Open communications at all levels.
- Empower employees to speak up and take action.
- Encourage management to lead by example.
- Verify actions with inspectors during audits.
- Maintain ongoing food safety culture assessments.
- Build culture champions.
Employee support is a key ingredient of a mature food safety culture. Food safety becomes a personal issue when employees connect their work to the foods their friends and family eat.
Rather than telling employees they must wash their hands, and wear gloves and hairnets, explain how those actions ensure food safety and mitigate risks. Make the “why” part of your food safety training and celebrate employees who identify and report food safety risks.
Enable employees to suggest improvements and identify risks. Listen and allow them to share their concerns about food safety risks. Empower employees to say something when they see something. And give them the authority to shut down production if they have a food safety concern.
Motivating and inspiring frontline workers about food safety is difficult if management doesn’t care equally. Food safety and risk mitigation should be a unifying cause everyone cares about. Also, senior management can be held liable during lawsuits or even charged with a crime if the company sickens consumers through negligence. Senior management should be aware of the state of food safety and routinely review food safety data with teams.
When working with auditors during an inspection, verify you’re maintaining a serious approach to food safety. Your written programs should describe what you’re doing and provide proof of your actions. Make sure your records are complete, accurate, and timely. In addition to your risk assessments and corrective actions, you must demonstrate that your training is current and that employees have completed courses and comprehended the training. Internal audits should be your best friend to help discover and address issues before inspectors find them.
Culture assessments measure a food safety culture’s maturity, providing insights into how well you’re managing hazards and risks. When conducted properly, they can help predict outcomes of controls versus a culture of responding to unexpected emergencies.
Annual assessments should be conducted two to four times a year to help create a baseline to build upon. The assessments process is a powerful tool that measures food safety across the entire organization, from senior management to frontline workers. Pulse surveys go even further by frequently measuring the impact of culture mitigation strategies.
You can lead your risk mitigation efforts by building food safety champions who can measure the effectiveness of your food safety culture and enable positive change. They can help verify employees are competent around food safety hazards and champion your efforts through ongoing education and outreach.
If you’d like to learn how to develop and promote a risk mitigation mindset in your organization, check out:
- SQF Risk Management course collection – these seven official SQF courses dive deep into the most critical areas of risk management
- Risk Assessment Course – discover key risk methodologies to ensure regulatory compliance